One stop shop market
Consumer Goods
Antien masterbatches, colors and additives are used in a variety of consumer goods applications such as oil cans and bottle closures, shampoo & detergent bottles, with complete range of thermoformed consumer products. Antien high performance and reliable products are the first choice in applications where consumers seek high level of consistency durability, convenience and concerns about freshness or deterioration of products
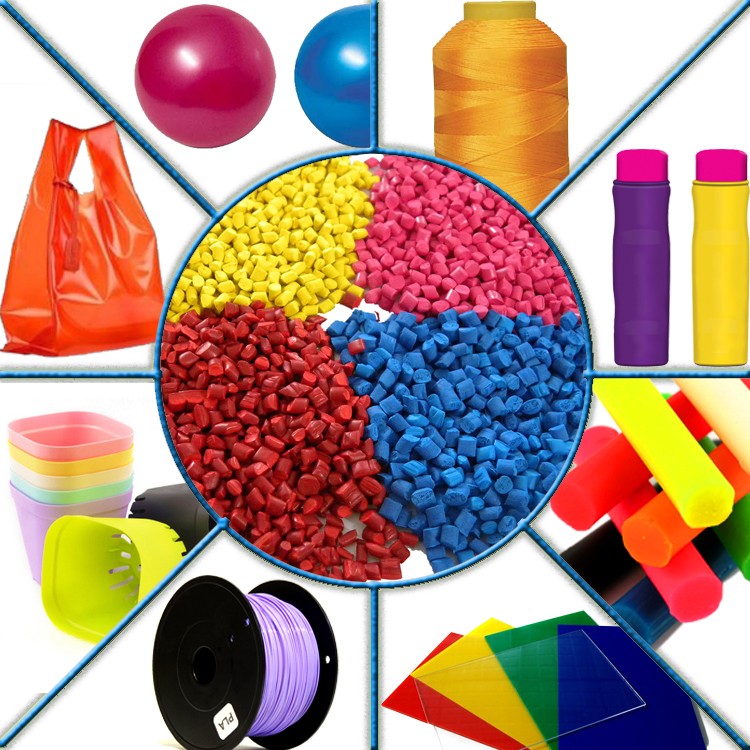
Flexible and Industrial Packaging
Antien has been offering all the segments of the packaging industry for more than 10 years in Vietnam and Worldwide. Flexible or rigid, blown or cast, lamination or extrusion. Our solutions for applications include, but are not limited to: PE, PP blown molding films, casting film, raffia, sheets, containers or boxes such as Soap & Shampoo Bottles, PET Bottles, Closures and Caps, Single beside some widen products as Multilayer Packaging, BOPP Packaging, Pallets, Automotive lubricant containers etc
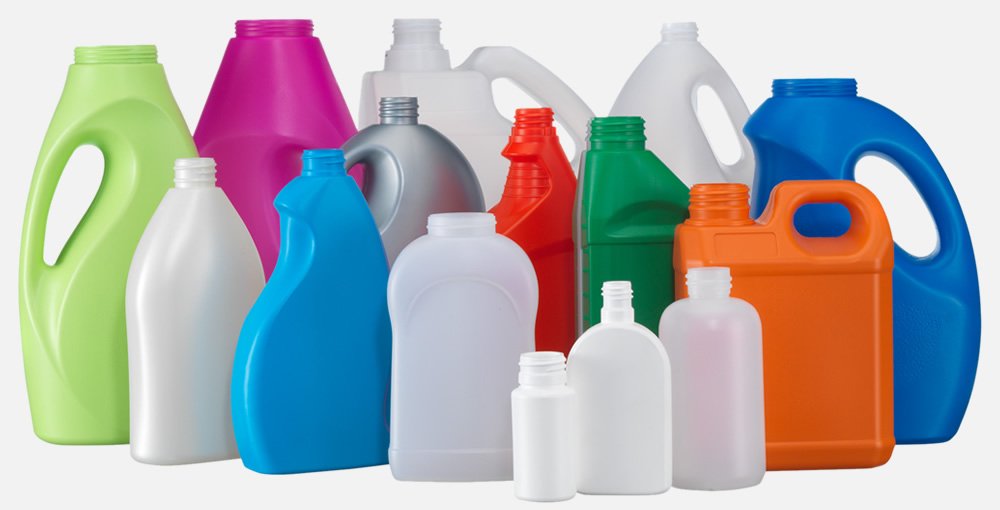
Agriculture/Plasticulture, Infrastructure & Industrial Products
More than one decades have seen remarkable development of plastic use in Agriculture and Industrials. The result has been an increase in productivity and crop yield round the year. Our wide-ranging additives provide a series of purposeful benefits for agricultural based products and processes. Our specially tailored masterbatches, additives and compounds are used in: shopping films, Mulch films, Woven, Non-woven, Automotives, Industrial spare-parts and Agrotextile etc
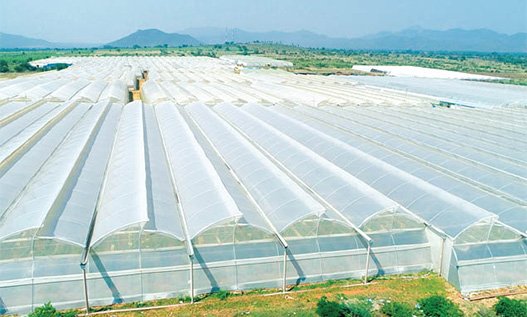
Biodegradable and Compostable
In addition to recovering energy and recycling, industrial composting (organic restoration/ organic recycling), using biodegradable and composting products such as bio-bags, packaging for fresh food, or disposable tableware and cutlery, becomes a choice of life. Antien bio compound, bio masterbatch are made from bio materials that are completely biodegradable by microorganisms into water, CO2, organic humus in natural or industrial environments and are not harmful to the environment, school surrounding.
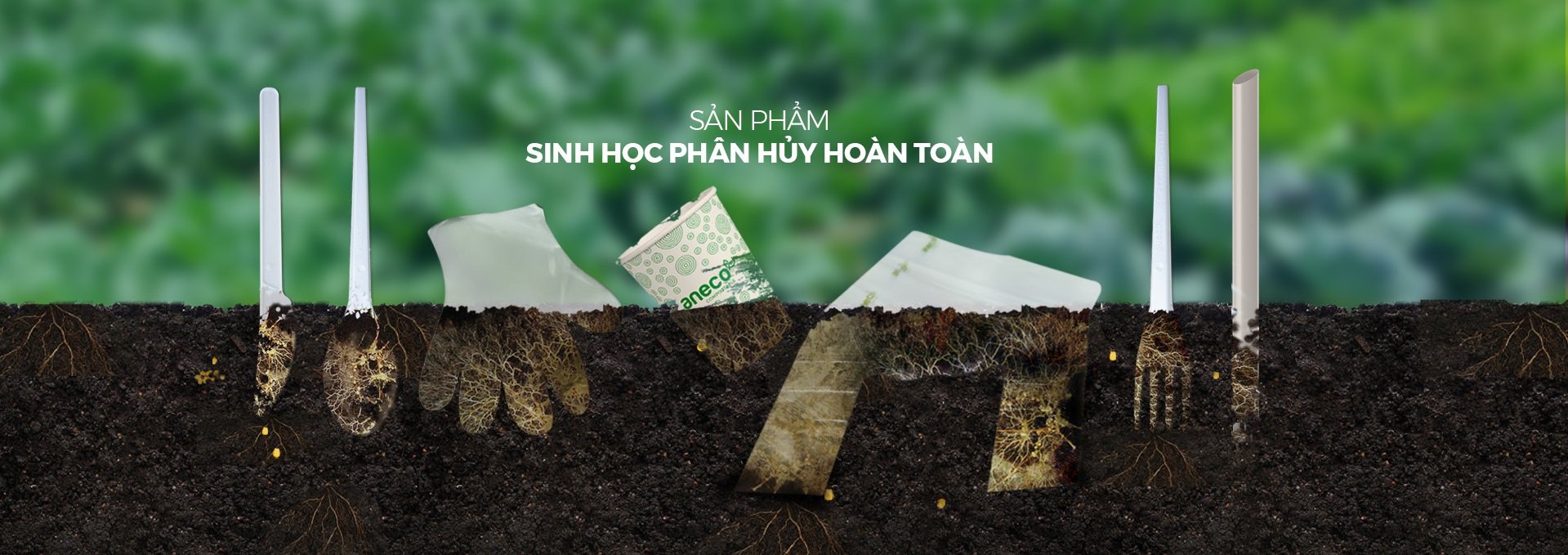